The UAW Strike: What will it mean for supply chains? And how can we weather the storm?
There is a general consensus among most economists that a short-lived United Autoworkers (UAW) Strike will probably have limited consequences for supply chains.
For one, these last few years have been wrought with supply chain shortages that could leave automakers reticent to cancel orders with their suppliers, at least initially.
Likewise, layoffs should be slow to occur as well. The tight labor market makes most companies rightly wary of laying off workers.
However, as the strike drags on—and it is already in its second week—we are likely to see order cancellations begin to bottleneck supply chains.
What can Tier 2 and Tier 3 suppliers do to mitigate some of these issues? To be certain, the biggest risk in the supply chains are these smaller companies with fewer resources and small bank accounts. But smaller companies also have the benefit of dexterity that many larger corporations do not.
Diversification
One key to resilience that Fastco has learned through the years and has made a strategic priority is diversification. Keeping all of your eggs in a basket like the automotive industry can be fatal for a company. Not only that, it is important to have a variety of customers even within a given industry. In automotive, this means diversifying outside of the Big Three to OEMs like Honda, Nissan, and Tesla.
Communication
But diversification is not something that a company can achieve overnight. As a result, it is imperative for companies that rely heavily on the automotive industry communicate with their customers in automotive and outside of automotive. Within the auto industry, we should be asking about upcoming demand and forecasting. Do the Tier 1 suppliers plan to use this time as an opportunity to build up a backlog? Or will they immediately be cancelling orders? Likely, there will be a combination of responses that will shift and change throughout the strike, if it is long-lasting.
Outside of the industry, we should be striving to expand our business. We should be asking for new opportunities and ways that our companies can add value for our customers. In short, we should be taking this time to seriously try and grow in industries outside of automotive.
Finally, we should be communicating internally with our team members and relying on their knowledge and expertise to help us figure out how to weather this storm.
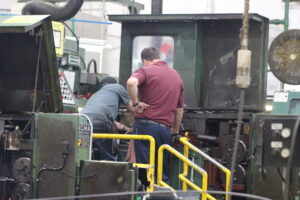
Cooperation
At Fastco, we have many team members who have worked through strikes and economic downturns over the last 50+ years that we have been around. A company is as resilient as its workforce, and we are lucky to have a resilient one.
Companies that only rely on the decision making power of a CEO are missing a key component of what it will take to successfully ride out an extended strike: cooperation.
Innovation
All of these things require innovation. We need to be thinking outside of the norm because these are not normal times.
Strikes are the growing pains of a tight labor market and an expanding middle class. They are likely to become more frequent as American manufacturing continues its comeback. It is important to have mitigation strategies in place to not only survive a strike but to thrive in its aftermath.