New Equipment at Fastco
This year, Fastco has added / is adding three new (to us machines). Here’s a breakdown of each machine.
New Cold Heading Equipment: Nakashimada NP-121
In the spring, we onboarded a Nakashimada NP-121. We were able to find this gem with the help of FH Machinery out of Pennsylvania (Thanks John!). These machines are rarely produced, and it is even harder to find a used machine in decent shape.
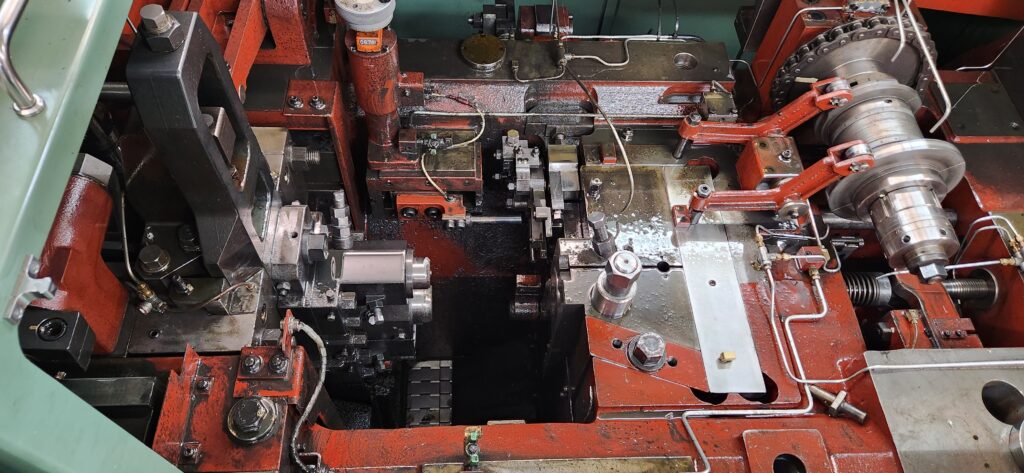
The machine ended up getting is the equivalent of finding a unicorn that is being ridden by leprechaun. What I’m trying to say is this was an exceptionally rare find. This machine in particular was delivered to the former owner as a brand new machine in 2019 and only ran periodically, which means it has very few hours of run time on it. This was a machine type that Fastco had been looking for to strategically add both capacity and capability, and we hit the used machine jackpot.
We currently have two Nakashimada NP-100 (2 die 3 blow) cold formers that stay very busy. The addition of another 2 die 3 blow machine adds capacity, and the increased size of the new machine allows us to quote larger parts that have a geometry that is appropriate for this type of forming sequence. The big advantage to 2 die 3 blow machines is the second punch (hammer) transfers the first station blank to the second (final forming) die. When loading the 1st station blank into the 2nd die, you are able to upset the head stock, allowing for a greater deformation ratio before the 3rd punch (final hit) forms the head / drive geometry. Also, by using the 2nd punch as the transfer mechanism, you are able to run parts that would be very difficult to transfer on a standard progressive cold former.
New Equipment in Thread Roll: Saspi #40
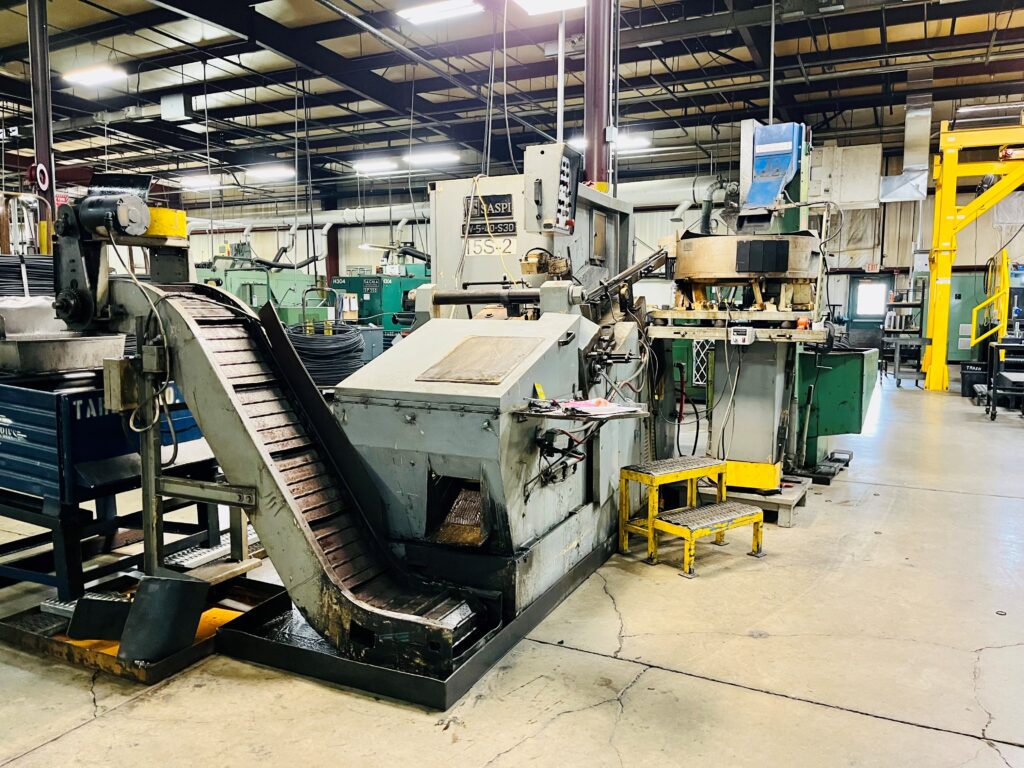
This year, Fastco also procured and began using a new (to us) Saspi #40. This machine provides us with some additional capabilities. More importantly, the machine’s location will help streamline our manufacturing process. This roller is set up in the middle of our cold heading west bay. There, it will be the second half of a manufacturing unit with our 6-die Jern Yao.
This shift to a cellular manufacturing setup for our largest parts will help reduce downtime. It will also create a more efficient and cost-effective manufacturing process.
Coming Soon: Ingramatic #50
Finally, we are excited for the impending delivery and installation of a new (to Fastco) Ingramatic RP7 #50 thread roller. In addition to gains in capability, we will increase our annual capacity for larger parts by 4-5 million parts per shift.
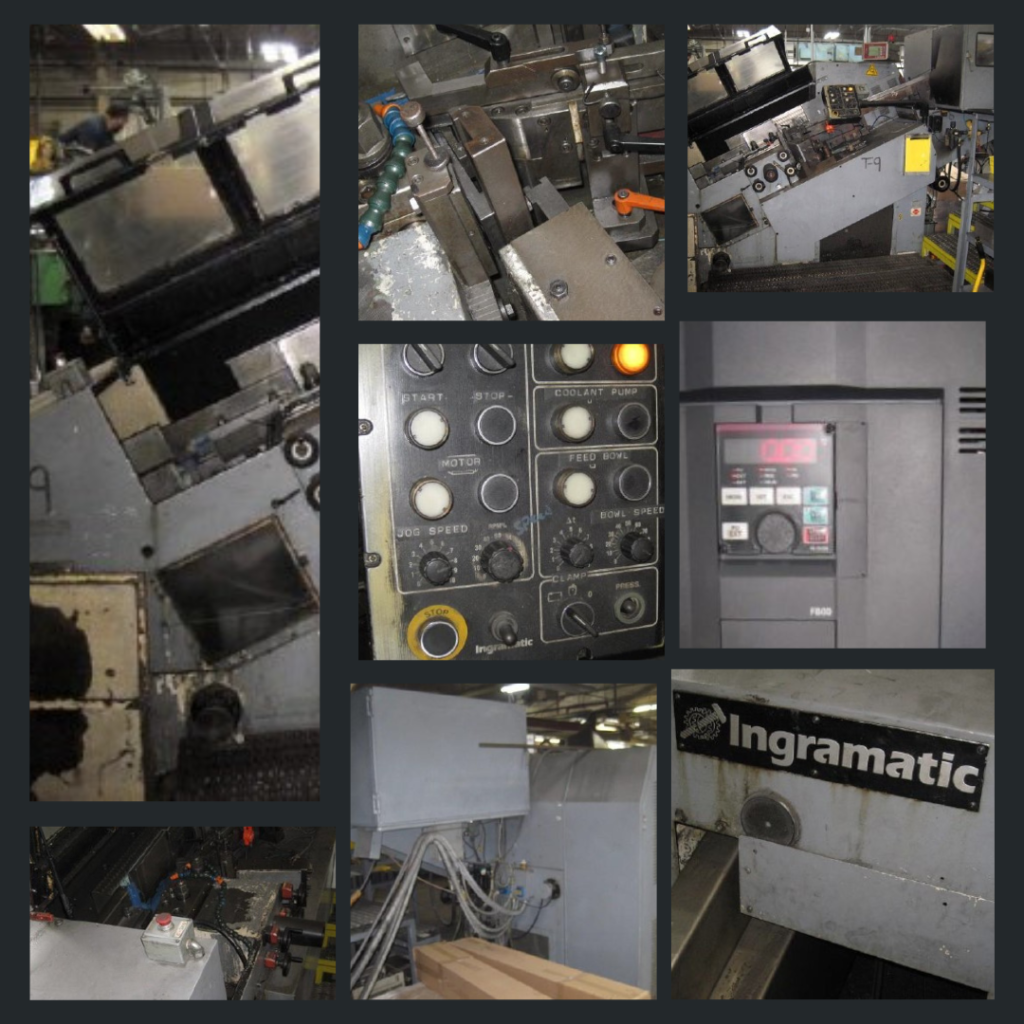
In terms of capabilities, this thread roller will allow us to roll up to 6” of M20 threads. This is slightly over what we are currently capable of cold forming. Having a machine of this size allows a safety factor on the size of blank we are able to roll without causing undue stress on this machine. This roller has a variable frequency drive. With this, we can roll at a maximum of 120 parts per minute. We should also be able to run current #40 size thread rolling parts with #50 dies at a faster PPM, allowing us to be more efficient with existing work. With the larger #50 roll dies, we will get more revolutions to make the threads. This translates into better die life and speed by spreading the stress over a larger surface area.
by Josh Symon (Engineering Manager), Jonathan Wright (Manufacturing Manager), and Bethany Tap